When Star Body Works, a four-shop regional MSO in Southern Oregon that also has a suspension calibration shop and a towing business, decided to expand its repertoire to include auto glass services, General Manager Jake Jennings asked around for recommendations on the best way to do it.
“They all said, ‘Hands down, Equalizer,’” Jennings said.
Jennings and three other Star Body Works employees have since completed Equalizer’s one-week, 40-hour course at its Auto Glass Academy in Round Rock, TX, taught by Global Education Director Gilbert Gutierrez. After hiring another employee who already had experience in auto glass, Star Body Works can now keep all its collision repair facilities’ glass work in house---saving money and cycle time.
Star Body Works
Medford and Grants Pass, OR
541-779-5621
starbodyworks.com
Company At A Glance...
Type: Collision Repair, Glass Replacement
Facility Employees: 65
In Business Since: 1948
Number of Locations: Four
Combined Production Space: 65,000 square feet
Star Body Works repairs an average of 450 cars per month between its four I-CAR Gold Class locations in Medford and Grants Pass, OR. The shops hold numerous OEM certifications, including Tesla, Subaru, Honda, Acura, Nissan, GM, Ford, Volvo, Chrysler, Kia, Hyundai and Mazda, and is close to achieving Mercedes-Benz.
Jennings said the shops pull away all glass from any panels being painted, for a factory-like finish that doesn’t expose paint lines to UV rays. “That’s almost every car if we’re doing a quarter panel, lift gate or pillar,” Jennings said.
Before, Star Body Works sublet that work to a mobile glass company that visited all four shops nearly every day. Now, it has its own van, staffed by its employees, who can do all the glass work themselves.
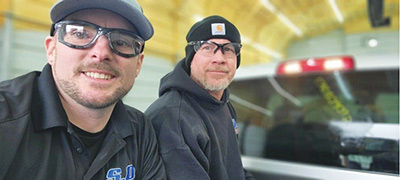
Jennings said bringing glass work in-house has several advantages.
First, the shop can make a bit of a profit off glass work now. When it was subletting the work, insurance companies would not allow Star Body Works to charge them any more than Star paid the mobile glass tech. “If I keep that in house, now I pay a labor cost, but I can make a profit off of it,” Jennings said.
Second, the shop has more control over scheduling repairs and replacements. “The glass industry is stretched so thin with how much work is out there,” Jennings said. “Two years ago, we could get (the sublet company) in same day (to do glass work.) Now, it’s two to three days minimum.”
Jennings said that is only going to get worse, as several glass companies are leaving the collision repair industry because insurance companies are putting pressure on how much shops are allowed to charge for the work. The 30-square-mile area of Oregon where his shops are located is down to only one such company.
Third, Star Body Works can ensure calibrations are correctly performed on its customers’ cars, which is becoming increasingly important in glass work.
“People who’ve been doing (auto glass) for 20 years don’t understand the importance of recalibrations, and it’s putting lives in danger,” Jennings said. “That’s the shadow lurking behind the windshield business.”
Jennings said he reached out to Shannon Kern, education program director at Equalizer, to find out what it would take to get trained. Soon after, he and another employee went to Texas for the one-week course. Jennings, who started in the collision repair industry with a high school internship more than 20 years ago, said the course “was a lot more than people anticipate,” but he saw students who started with no knowledge of the industry build their skills as quickly as people who already had years under their belts.

Over the five days, the students learned about laws related to glass repair and replacement and were taught---both in the classroom and in a hands-on shop---how to correctly prepare a vehicle, including pre-scanning ADAS features, and perform the work. The course was capped off by a final written test and a hands-on replacement observed by instructors.
When the students passed the final, they were certified by Equalizer and eligible to take the national certification test, which Jennings also passed.
Equalizer also gives students a tuition credit to purchase tools, which Jennings took full advantage of. He said Star Body Works uses the Viper and Raptor cord and wire glass removal tools, as well as Equalizer’s glass stands, knives and chip and crack repair tool.
“I like the tools and the way they work,” Jennings said. “You know they’re going to have the tool that works the best. All their tools work together.”
Jennings said he has only had to send back one tool to be repaired, which Equalizer did, under warranty, and returned in two days.
“We get really good support,” Jennings said. “I’m constantly ordering stuff from them. They know me and answer with ‘Hey Jake.’”
Equalizer® Industries, Inc.
512-388-7715
www.Equalizer.com
www.autoglassacademy.com
Facebook: @equalizertools
Twitter: @equalizertools
Instagram: @equalizertools
YouTube: @equalizervideo
To read more auto body shop profiles in the June 2023 Shop and Product Showcase, click here.